Is it really a production line?
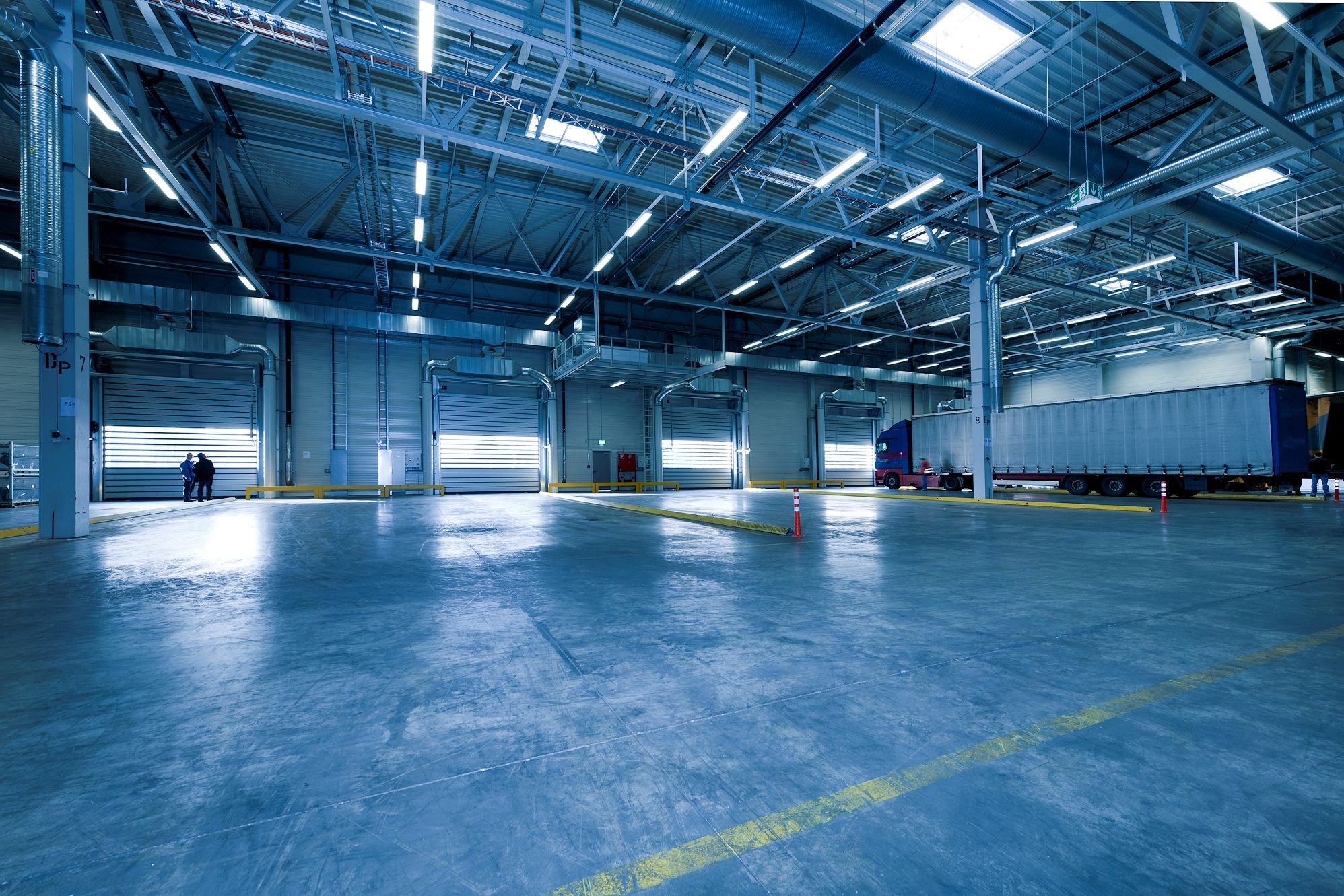
I have mentioned several times in my previous posts that a digital service is a production line. It is time today to exercise the idea to understand the specificities that appear when deploying a digital product.
Digital production line
So, what is a production line?
The definition from Collins Dictionary is
A production line is a factory system in which parts or components of the end product are transported by a conveyor through a number of different sites at each of which a manual or machine operation is performed on them without interrupting the flow of production
In this definition, 3 main notions are highlighted:
- A purposed flow of operations that shall not be interrupted
- A creation of a final product from parts
- A set of operations to be performed manually or automatically
Of course, the first image that comes to our mind with this definition is either the modern production lines of automotive with lines of automatic arms or the Fordist assembly lines that Chaplin featured in the movie Modern Time.
But, if we step back, the goal of a digital service is to create output data from inputs by applying intermediate transformations (that can include data memorization, profiling, matching …)
So, we could transform slightly the definition of production line by saying:
A digital production line is a factory system in which parts or data fragment of the end products are transported by digital pipelines through a number of different sites at each of which a manual or machine operation is performed on them without interrupting the flow of production
With this view, we see that the components of the digital service and its behavior needs to be monitored and, its overall productivity needs to be measured to assess the return of investments and total cost of ownership (TCO) of the service.
Like a production line, the digital production line will rely on the availability of internal (sensors) and external resources (IAAS/PAAS/SAAS) to create the final data product. The deficiency of a 3rd party data source will create either an interruption of the production line (undersupply) or product non conformity (quality).
In term of evolution, both production lines have to manage the same challenge
- update the different sites to process or produce new part of the product
- update the existing stock (physical stock or data stored)
- inform the users of the product of compatibility/incompatibility of interfaces
Now, to analyze more deeply, let’s look at two scenarios:
- An Industry 4.0 digital service created to monitor a real production process
- A consumer digital service that delivers a service to a user
The first scenario will focus on the analogy of values with a physical production line, the second will look at the elements that surround the production line but drives its operation.
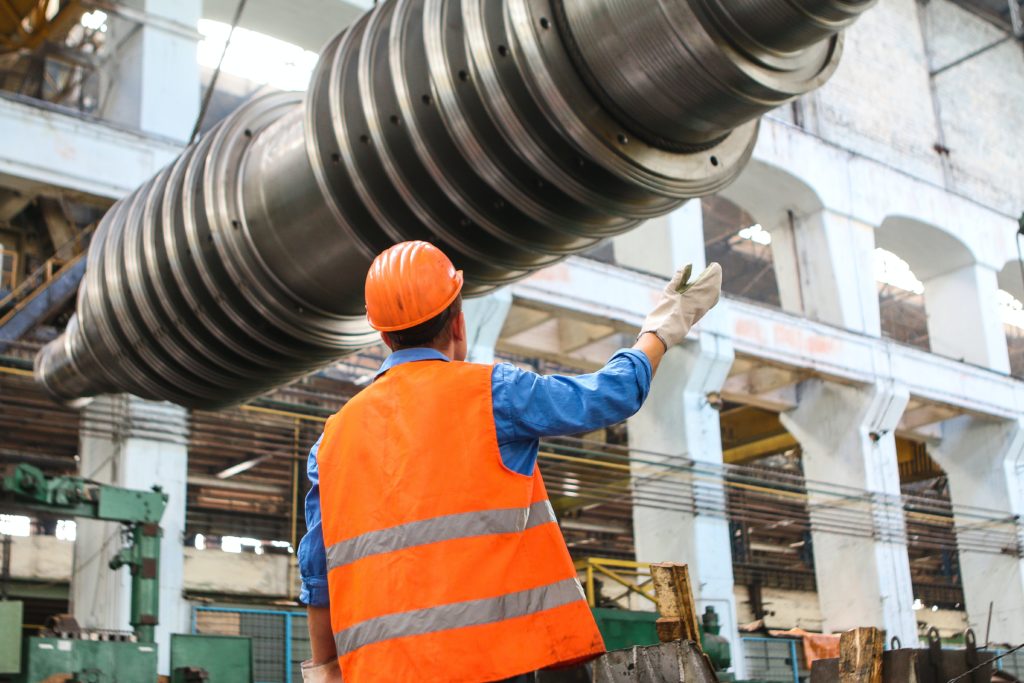
Industry 4.0 digital service
As we modernize physical production lines, we add sensors and solutions that can track products, measure productivity and any other kind of enhancement powered by data.
For this kind of digital service, the goal is to serve the physical production line by detecting anomalies, triggering planned or reactive actions (data for action). The data created by the digital service is not for an external customer and do not have a direct value for sale. But the service is still delivering highly valuable as it drives the activity of the physical production line; it is a digital production line based on physical sensors, data processing and reports/alerts output.
To understand the impact of deficiencies, lets classify them with the 3 dimensions of Overall Equipment Effectiveness – OEEE (see more on this link):
- Availability
- Impossibility to measure the stock and supply chain inputs
- Impossibility to assign efficient priorities in regards to production objectives
- Impossibility to communicate or alert team members
- Performance
- Latency in the communication of information or trigger of actions
- Loss of real-time information that cannot be processed when needed
- Infrastructure cost of inappropriate provisioning
- Quality
- Incorrect measures or report of the production objectives
- Trigger of inappropriate decisions
- Waste of time and materials to investigate or react to inappropriate interactions.
As data quality impact is often underestimated, let me tell you a story.
A few days ago, I subscribed to a home service and scheduled an appointment online. The system called me three days before the appointment to remind me of the service and texted me also. But, as the system was wrongly configured, it did not process my acknowledge and started to send me a notification every 2h … until I called the support service to manually disactivate the reminder.
In production, this kind of behavior will overwarm the team and reduced its efficient to the point where they will even ignore the system.
In this scenario, the cost of the digital production line is indirect by creation of rework, wrong decisions by lack of information, and distracted team in their daily activity.
From a capacity perspective, the demand is based on the volume of data created by the production line. This volume is related to:
- The installed sensors on the physical production line
- The cadence of production
- The volume of data created: (good count * report size) + (defects * defect diagnostic size)
As we can see, if the production line is stable, the capacity of the digital production line can be predicted and anticipated.
The digital service will scale at the same rhythm than the physical production line, based on growth, reduction or improvement of the process
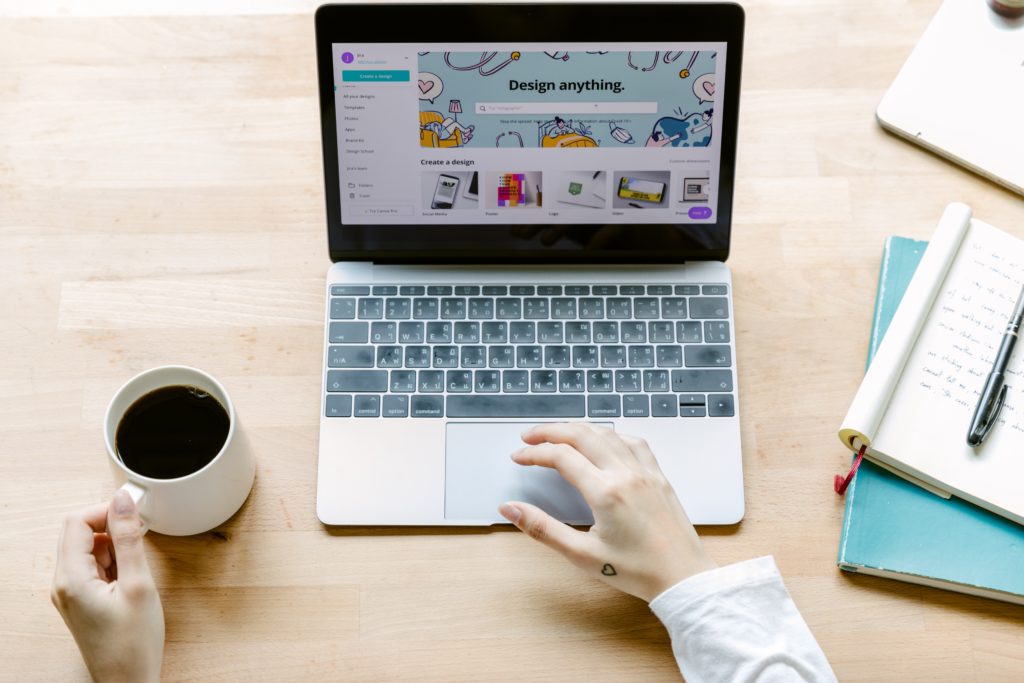
Consumer digital service
A consumer digital service can process data coming from others services (like a payment transaction) or from the user (like a video processing). For both, the trigger of the digital service is influenced by event sources that are not under the control of your company.
This implies two important assumptions
- The quality of the inputs is not guaranteed and in average lower than data procured through industrial processes
- The demand will fluctuate based on the user actions and can only partially be predicted.
In term of deficiencies, the impacts will be:
- Availability
- Create frustration of the user that cannot access its data
- Generate side effects on input or output (for example cancelling a payment)
- Have the user select a concurrent service
- Performance
- Latency in the communication of information or trigger of actions
- Loss of real-time information that cannot be processed when needed
- Low margin as the internal cost is too high
- Quality
- Lack of trust from the user and request of reimbursement
- Side effect on connected systems (for example wrong amount processed)
- Incorrect reporting or summary to the user
In this scenario, as the system relies more on the user behavior, the performance (or lack of) is difficult to perceive for the user : Who has never complained to their IT that the company network was not working from their home ignoring that their own service provider was having a defective equipment?
Also, even if the user is responsible for the quality of its data, he will expect the system to detect data inconsistency and prevent side effect of wrong inputs (like ordering 10 000 pizzas).
The main challenge of consumer service is to build an accurate behavior model that can predict the demand, and, a scaling model that allow the solution to evolve with the demand.
The demand model (average behavior, daily variation, seasonal variation …) will be converted to a capacity planning (fixed and scaled capacity). The accuracy of the capacity planning in regards to the real demand will strongly impact the dataflow, cost and performance of the service.
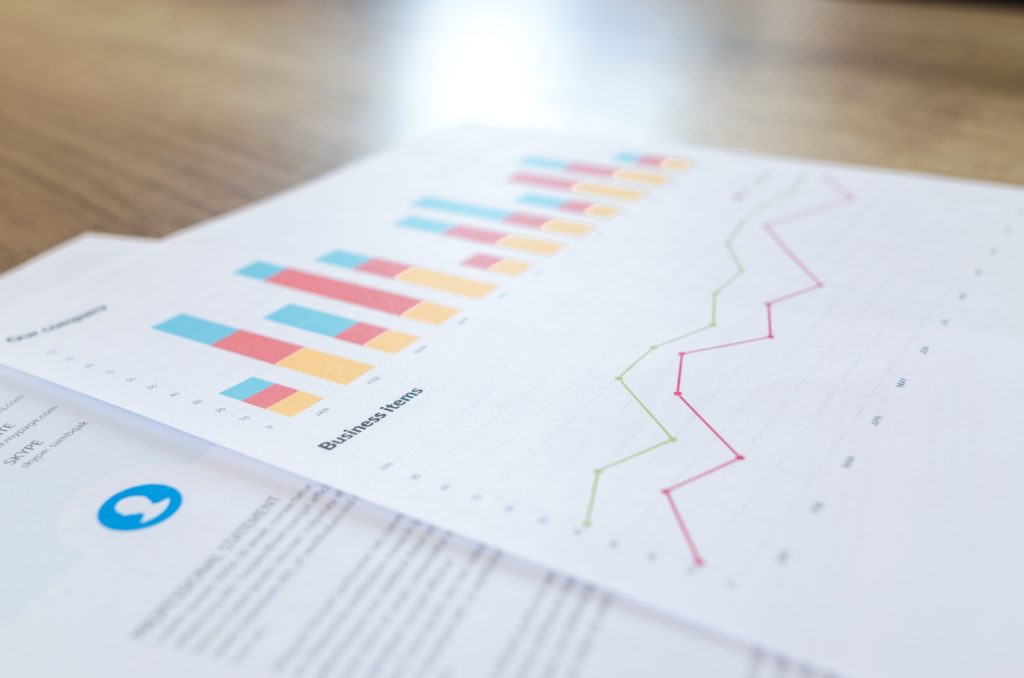
So, is it that different?
After reviewing those two scenarios and the similarity with physical production lines, let’s look at major differences
- Persistence
A physical production line needs time to be implanted in a facility
A digital production line should be created on demand and deprovisioned as soon as the demand disappear. - Scalability
Even with a mature blueprint, a physical production line needs physical investment to scale and has a cost of deprovisioning
A digital production line should scale with the demand by leveraging cloud capacities and have its minimum size as small as possible - Capacity
A physical production line shall have a provisioning capacity available for delivery rush or for the maximum volume need
A digital production line shall always have the smaller difference between provisioned and used capacity as renting resources without using them is a waste.
To simplify, a production line plan is often driven by capital investment whereas a digital production line is driven by instant demand (like a restaurant where food is wasted if not used).
This difference implies to have the architecture model of a digital service highly attentive to the demand and its evolution. The profitability and performance of the digital service needs to be assessed dynamically and adjustments needs to occur at a higher rate than a physical production line