Optimization of maintenance schedule
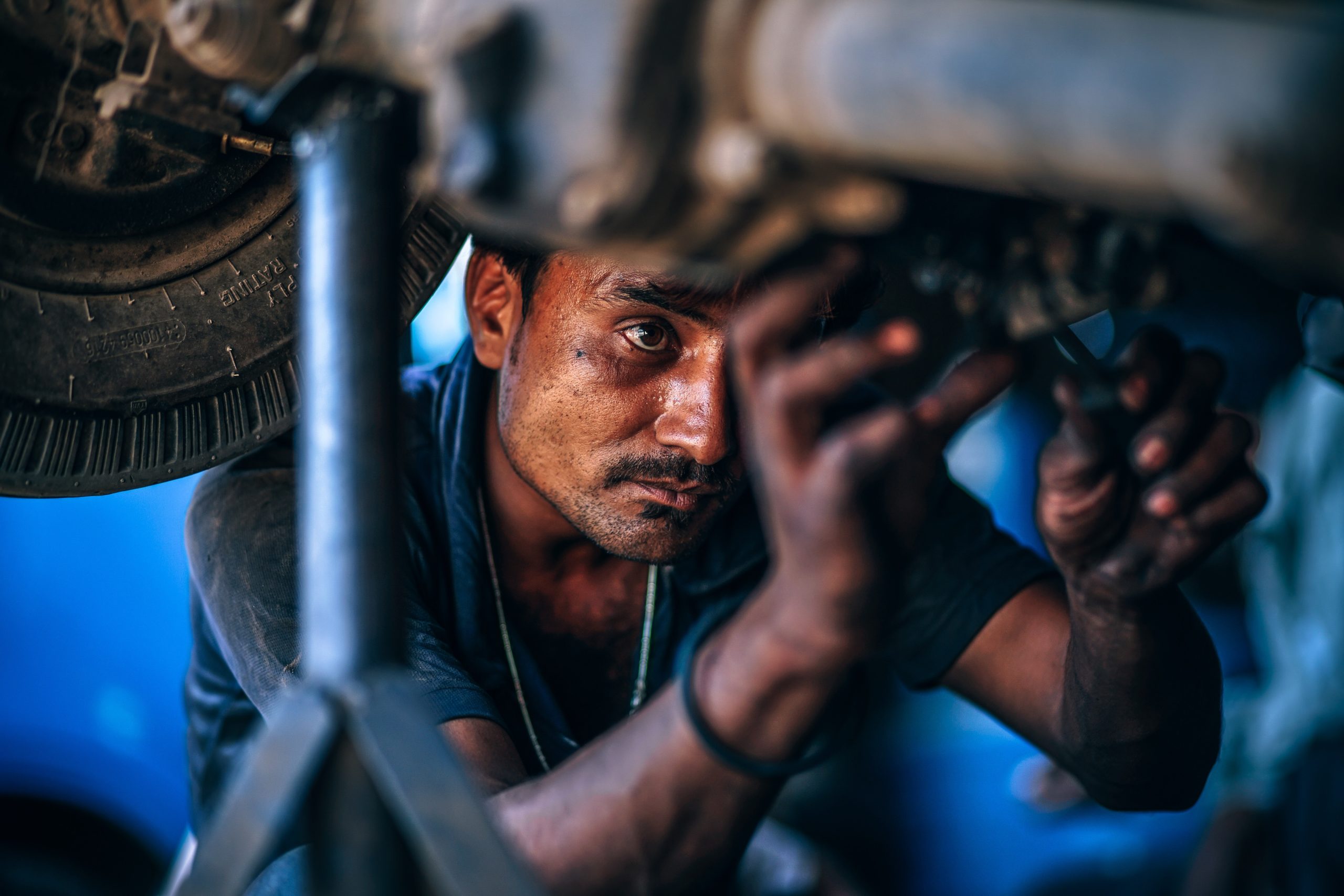
When operating a fleet of aircraft, an airline needs to plan for its maintenance operation.
Each aircraft has a set of scheduled operation for its own need (engine, structure …) but also for the cabin services (IFE, connectivity …).
The optimization of those activities have a dimensional impact on the availability of the fleet and on the overall cost of ownership.
The approach of the data optimization presented in the tech talk How to have a profitable digital service for data operation ? can also be applied on the optimization of the maintenance operation.
For a similar pattern of value creation, the optimization of the maintenance will target to optimize the resources (man/material) needed to perform the operation.
Maintenance operation can be define as a set of unitary operation.
Each operation :
- impact a part of the full system (LRU, SRU, …)
- has an average or bounded time to perform
- need a specific expertise
- can expect other mandatory operations to be performed before
The optimization can be then separated into 2 objectives that will then (like data flow) be combined for final schedule :
- predicted or scheduled maintenance
- on demand maintenance after incident
To avoid lost of service, most systems find return of investment on the first subject but the benefits of the time invested in the analysis is always related to the expected SLA and importance of the service.
Looking at the optimization of maintenance operation, we will not focus on the algorithms used to predict incoming failure and assuming for now that the system is able to do it.
This brings back the predictive maintenance (to avoid failure) as one use case of scheduled maintenance.
The characteristic of scheduled maintenance is that there is a clear identification of the 4 operation information.
For on demand maintenance, the operation needs to be inserted on top of the existing schedule by a specific insertion algorithm that will take into account the priority of the operation compared to the existing pre-planned ones.
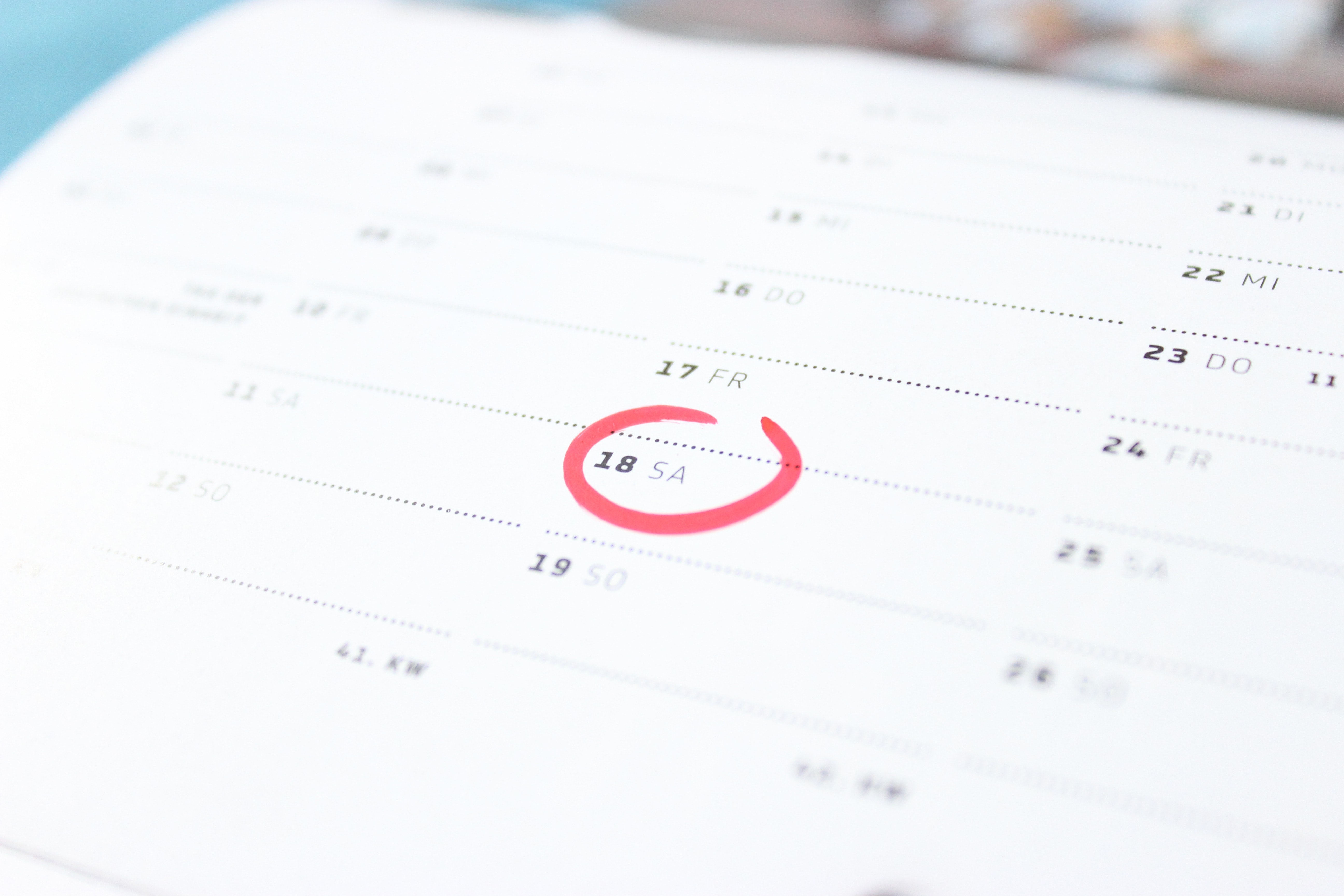
As these scheduling activity could be standard, the other dimension of the maintenance operation of an aircraft fleet is the geographical availability : the aircraft, parts and technicians have to be at the same location at the same time to perform the operation.
This dimension involve strategy of pre-provisioning (to optimize shipping), optimization by predictive demand and tracking of agents for optimization of their travels.
This is the kind of optimization needed to offer services like Amazon Prime in 48h or 24h.
In our domain, optimization of operation will also imply to facilitate the activity before (airport access, aircraft access …) and after (transfer to repair center, generation of the maintenance report).
Finally, like many other services, the high mobility of the aircraft impact the process of optimization of operation.
The inability to perform an operation on time, whereas needed on a single aircraft, will impact, most of the time, another operation team as the aircraft can not be brought back rapidly where its maintenance was scheduled.
For example, if a seat display has to be replaced at LAX, the maintenance will have to happen at the next stop in Dubai if a team (and a spare seat) is available there.
Reducing the spares for LRU and optimizing the agenda of the maintenance team is a direct return of investment on the field.
As maintenance and transmission plan will have conflicting interest, another optimization value can be found later by combining both in the consolidated optimized schedule.